ПОРОШКОВАЯ ОКРАСКА
ПОРОШКОВАЯ ОКРАСКА — передовой метод получения защитно-декоративных покрытий разнообразных материалов и изделий, которые используются как производителями, так и потребителями. В результате применения порошковой окраски получается однородное, прочное, высококачественное покрытие с высоким физико-механическими, химическими, защитными свойствами.
Нанесение порошковых полимерных покрытий (порошковая окраска) применяется как альтернатива нанесения жидких лакокрасочных материалов.
подготовка поверхности изделий; нанесение порошковых покрытий в электростатическом поле; формирование покрытий в печах.
В начальной стадии любого процесса окрашивания производится предварительная обработка поверхности. Это самый трудоемкий и продолжительный процесс, которому часто не уделяют должного внимания, однако который является необходимым условием получения качественного покрытия. Подготовка поверхности предопределяет качество, стойкость, эластичность и долговечность покрытия, способствует оптимальному сцеплению порошковой краски с окрашиваемой поверхностью и улучшению его антикоррозийных свойств.
При удалении загрязнений с поверхности важно наиболее правильно подобрать метод обработки и состав, применяемый для этой цели. Их выбор зависит от материала обрабатываемой поверхности, вида, степени загрязнения, а также требованиями к условиям и срокам эксплуатации.
Для предварительной обработки поверхности перед окрашиванием используются методы обезжиривания, удаления окисных пленок (абразивная очистка, травление) и нанесения конверсионного слоя (фосфатирование, хроматирование). Из них обязателен лишь первый метод, а остальные применяются в зависимости от конкретных условий.
очистка и обезжиривание поверхности; фосфатирование (фосфатами железа или цинка); споласкивание и закрепление; сушка покрытия.
На первом этапе происходит обезжиривание и очистка обрабатываемой поверхности. Она может производиться механическим или химическим способом. При механической очистке используются стальные щетки или шлифовальные диски, также в зависимости от размеров поверхности возможна ее притирка чистой тканью, смоченной в растворителе. Химическая очистка осуществляется с использованием щелочных, кислотных или нейтральных веществ, а также растворителей, применяющихся от вида и степени загрязнения, типа материала и размера обрабатываемой поверхности и т.д.
При обработке химическим составом детали могут погружаться в ванну с раствором или подвергаться струйной обработке (раствор подается под давлением через специальное отверстие). В последнем случае эффективность обработки значительно повышается, поскольку поверхность подвергается еще и механическому воздействию, к тому же осуществляется непрерывное поступление чистого раствора к поверхности.
Нанесение конверсионного подслоя предотвращает попадание под покрытие влаги и загрязнений, вызывающих отслаивание и дальнейшее разрушение покрытия.
Фосфатирование и хроматирование обрабатываемой поверхности с нанесением тонкого слоя неорганической краски способствует улучшение адгезии поверхности с краской и предотвращает ее от ржавчины, повышая ее антикоррозийные свойства. Обычно поверхность обрабатывается фосфатом железа (для стальных поверхностей), цинка (для гальванических элементов), хрома (для алюминиевых материалов) или марганца, а также хромового ангидрида. Для алюминия и его сплавов часто применяют методы хроматирования или анодирования. Обработка фосфатом цинка обеспечивает наилучшую защиту от коррозии, однако этот процесс более сложный, чем остальные. Фосфатирование может увеличить сцепление краски в 2-3 раза.
Для удаления окислов (к ним относятся окалина, ржавчина и окисные пленки) используется абразивная очистка (дробеструйная, дробеметная, механическая) и химическая очистка (травление).
Абразивная очистка осуществляется при помощи абразивных частиц (песка, дроби), стальных или чугунных гранул, а также скорлупы ореха, подающихся на поверхность с большой скоростью с помощью сжатого воздуха или при помощи центробежной силы. Такая очистка повышает адгезию покрытия.
Следует помнить, что абразивная очистка может применяться к материалам, толщина которых составляет более 3 мм. Большую роль играет правильный выбор материала, поскольку слишком крупная дробь может привести к большой шероховатости поверхности, и покрытие будет ложиться неравномерно.
Травление представляет собой удаление загрязнений, окислов и ржавчины путем применения травильных растворов на основе серной, соляной, фосфорной, азотной кислоты или едкого натра. Растворы содержат ингибиторы, которые замедляют растворение уже очищенных участков поверхности.
Химическая очистка отличается большей производительностью и простотой применения, чем абразивная, однако после нее необходимо промывать поверхность от растворов, что вызывает необходимость применения дополнительных очистных сооружений.
На заключительной стадии подготовки поверхности используется пассивирование поверхности, то есть ее обработка соединениями хрома и нитрата натрия. Пассивирование предотвращает появление вторичной коррозии. Его можно применять как после обезжиривания поверхности, так и после фосфатирования или хроматирования поверхности.
После споласкивания и сушки поверхность готова для нанесения порошкового покрытия.
? пневматическая транспортировка порошкового материала по шлангу от эжекторного насоса к распылителю,
? зарядка частиц порошкового материала зарядными устройствами распылителей,
? осаждение частиц порошка на изделие с образованием сплошного порошкового слоя.
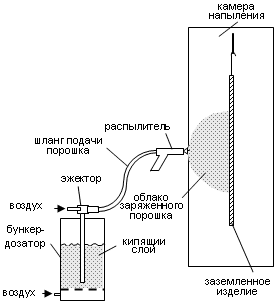
Забор порошкового материала из бункеров с кипящим слоем целесообразно использовать при больших производственных программах или при окраске только одним цветом. Забор порошка из насыпного слоя ("забор из коробки") предпочтительнее применять при небольших производственных программах и частой смене цвета порошкового материала
Зарядка частиц порошкового материала может осуществляться электростатическим или трибостатическим способами. При электростатическом способе зарядки частицы заряжаются ионами в поле коронного разряда, создаваемом высоковольтными электродами распылителя, что обеспечивает эффективную зарядку любых типов порошковых материалов. Трибостатическая зарядка осуществляется за счет трения порошкового материала о трибоэлектризующие конструкции распылителя. В конструкции распылителей при этом отсутствуют высоковольтные элементы, но зарядка при этом более чувствительна к степени осушки воздуха от влаги и к типам применяемых порошковых материалов.
При осаждении порошкового материала на изделие частицы проходят две зоны. Первая зона - это основной промежуток между распылителем и изделием. Здесь частицы порошка движутся в основном за счет потока воздуха по направлению к окрашиваемому участку поверхности изделия. Вторая зона - это узкий слой у поверхности изделия, где частицы порошка движутся в потоке воздуха, обтекающем изделие. Осаждение заряженных частиц порошка на поверхность изделия происходит под действием электрического поля. При образовании на поверхности изделия сплошного слоя порошка в нем начинают происходить процессы, препятствующие дальнейшему осаждению частиц на поверхность изделия. Таким образом, существует предельная толщина получаемого порошкового слоя, зависящая от величины заряда частиц в слое. Чем больше заряд, тем меньше предельная толщина слоя порошка.
При нанесении порошкового слоя на изделия сложной формы есть ряд особенностей в выборе режимов работы распылительного оборудования.
Процесс нанесения порошкового слоя на изделия осуществляется в установках нанесения покрытий, состоящих из окрасочных камер и систем рекуперации порошка.
Чаще всего процесс формирования покрытия осуществляется путем нагрева порошкового слоя до состояния его оплавления с образованием монолитного слоя. Нагрев изделия в печи оплавления и полимеризации осуществляется до температуры 140-220 °С в зависимости от вида краски. При последующей обработке в результате отверждения (для термореактивных материалов) или охлаждения (для термопластичных материалов) слоя образуется твердая пленка.
Процесс оплавления проходит в несколько стадий:
? сначала порошок проходит вязко-текучее состояние;
? затем проходит сплавление частиц порошка с образованием монолитного слоя;
? одновременно со сплавлением происходит смачивание покрываемой поверхности и растекание расплава полимера;
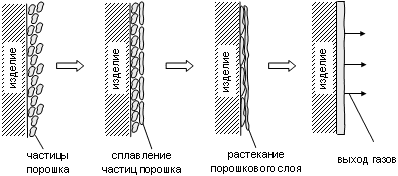
Отверждение покрытий на основе термореактивных материалов происходит в процессе теплового воздействия и длится вполне определенное время. Каждому покрываемому изделию соответствует оптимальный режим отверждения. Охлаждение покрытий на основе термореактивных материалов не влияет на свойства покрытия.
Для термопластов режим и среда охлаждения во многом определяют качество покрытия. В качестве охлаждающего агента используют воду, минеральные масла, применяют охлаждение на воздухе.
Для формирования покрытия используют:
? конвективную теплопередачу тепла от нагретого воздуха к изделию с порошковым слоем (конвективные печи). Оплавление порошкового слоя происходит с внешней стороны, что затрудняет выход газов из слоя. Данный способ обладает большой универсальностью и не зависит от формы изделия, но имеет повышенные энергетические затраты;
? инфракрасный нагрев изделия с порошковым слоем. Оплавление порошкового слоя происходит с внутренней стороны, что облегчает выход газов из слоя. Способ обладает низкими энергетическими затратами, но пригоден для изделий простой конфигурации.
Нанесение порошковых полимерных покрытий (порошковая окраска) применяется как альтернатива нанесения жидких лакокрасочных материалов.
Технология окраски порошковыми материалами включает три стадии:
В начальной стадии любого процесса окрашивания производится предварительная обработка поверхности. Это самый трудоемкий и продолжительный процесс, которому часто не уделяют должного внимания, однако который является необходимым условием получения качественного покрытия. Подготовка поверхности предопределяет качество, стойкость, эластичность и долговечность покрытия, способствует оптимальному сцеплению порошковой краски с окрашиваемой поверхностью и улучшению его антикоррозийных свойств.
При удалении загрязнений с поверхности важно наиболее правильно подобрать метод обработки и состав, применяемый для этой цели. Их выбор зависит от материала обрабатываемой поверхности, вида, степени загрязнения, а также требованиями к условиям и срокам эксплуатации.
Для предварительной обработки поверхности перед окрашиванием используются методы обезжиривания, удаления окисных пленок (абразивная очистка, травление) и нанесения конверсионного слоя (фосфатирование, хроматирование). Из них обязателен лишь первый метод, а остальные применяются в зависимости от конкретных условий.
Процесс подготовки поверхности включает несколько этапов:
На первом этапе происходит обезжиривание и очистка обрабатываемой поверхности. Она может производиться механическим или химическим способом. При механической очистке используются стальные щетки или шлифовальные диски, также в зависимости от размеров поверхности возможна ее притирка чистой тканью, смоченной в растворителе. Химическая очистка осуществляется с использованием щелочных, кислотных или нейтральных веществ, а также растворителей, применяющихся от вида и степени загрязнения, типа материала и размера обрабатываемой поверхности и т.д.
При обработке химическим составом детали могут погружаться в ванну с раствором или подвергаться струйной обработке (раствор подается под давлением через специальное отверстие). В последнем случае эффективность обработки значительно повышается, поскольку поверхность подвергается еще и механическому воздействию, к тому же осуществляется непрерывное поступление чистого раствора к поверхности.
Нанесение конверсионного подслоя предотвращает попадание под покрытие влаги и загрязнений, вызывающих отслаивание и дальнейшее разрушение покрытия.
Фосфатирование и хроматирование обрабатываемой поверхности с нанесением тонкого слоя неорганической краски способствует улучшение адгезии поверхности с краской и предотвращает ее от ржавчины, повышая ее антикоррозийные свойства. Обычно поверхность обрабатывается фосфатом железа (для стальных поверхностей), цинка (для гальванических элементов), хрома (для алюминиевых материалов) или марганца, а также хромового ангидрида. Для алюминия и его сплавов часто применяют методы хроматирования или анодирования. Обработка фосфатом цинка обеспечивает наилучшую защиту от коррозии, однако этот процесс более сложный, чем остальные. Фосфатирование может увеличить сцепление краски в 2-3 раза.
Для удаления окислов (к ним относятся окалина, ржавчина и окисные пленки) используется абразивная очистка (дробеструйная, дробеметная, механическая) и химическая очистка (травление).
Абразивная очистка осуществляется при помощи абразивных частиц (песка, дроби), стальных или чугунных гранул, а также скорлупы ореха, подающихся на поверхность с большой скоростью с помощью сжатого воздуха или при помощи центробежной силы. Такая очистка повышает адгезию покрытия.
Следует помнить, что абразивная очистка может применяться к материалам, толщина которых составляет более 3 мм. Большую роль играет правильный выбор материала, поскольку слишком крупная дробь может привести к большой шероховатости поверхности, и покрытие будет ложиться неравномерно.
Травление представляет собой удаление загрязнений, окислов и ржавчины путем применения травильных растворов на основе серной, соляной, фосфорной, азотной кислоты или едкого натра. Растворы содержат ингибиторы, которые замедляют растворение уже очищенных участков поверхности.
Химическая очистка отличается большей производительностью и простотой применения, чем абразивная, однако после нее необходимо промывать поверхность от растворов, что вызывает необходимость применения дополнительных очистных сооружений.
На заключительной стадии подготовки поверхности используется пассивирование поверхности, то есть ее обработка соединениями хрома и нитрата натрия. Пассивирование предотвращает появление вторичной коррозии. Его можно применять как после обезжиривания поверхности, так и после фосфатирования или хроматирования поверхности.
После споласкивания и сушки поверхность готова для нанесения порошкового покрытия.
Нанесение порошковых покрытий в электростатическом поле.
С помощью распылительного оборудования осуществляется нанесение слоя частиц на поверхность изделия. При этом должна обеспечиваться высокая эффективность осаждения порошка на изделие, требуемая толщина и равномерность слоя по всей поверхности, а также возможность окрашивания заэкранированных частей изделия.Основные стадии процесса нанесения порошкового слоя:
? забор порошкового материала из насыпного или кипящего слоя с помощью эжекторного насоса,? пневматическая транспортировка порошкового материала по шлангу от эжекторного насоса к распылителю,
? зарядка частиц порошкового материала зарядными устройствами распылителей,
? осаждение частиц порошка на изделие с образованием сплошного порошкового слоя.
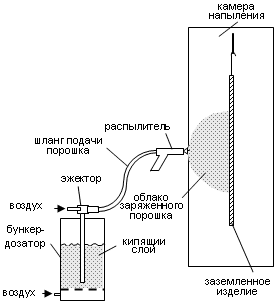
Забор порошкового материала из бункеров с кипящим слоем целесообразно использовать при больших производственных программах или при окраске только одним цветом. Забор порошка из насыпного слоя ("забор из коробки") предпочтительнее применять при небольших производственных программах и частой смене цвета порошкового материала
Зарядка частиц порошкового материала может осуществляться электростатическим или трибостатическим способами. При электростатическом способе зарядки частицы заряжаются ионами в поле коронного разряда, создаваемом высоковольтными электродами распылителя, что обеспечивает эффективную зарядку любых типов порошковых материалов. Трибостатическая зарядка осуществляется за счет трения порошкового материала о трибоэлектризующие конструкции распылителя. В конструкции распылителей при этом отсутствуют высоковольтные элементы, но зарядка при этом более чувствительна к степени осушки воздуха от влаги и к типам применяемых порошковых материалов.
При осаждении порошкового материала на изделие частицы проходят две зоны. Первая зона - это основной промежуток между распылителем и изделием. Здесь частицы порошка движутся в основном за счет потока воздуха по направлению к окрашиваемому участку поверхности изделия. Вторая зона - это узкий слой у поверхности изделия, где частицы порошка движутся в потоке воздуха, обтекающем изделие. Осаждение заряженных частиц порошка на поверхность изделия происходит под действием электрического поля. При образовании на поверхности изделия сплошного слоя порошка в нем начинают происходить процессы, препятствующие дальнейшему осаждению частиц на поверхность изделия. Таким образом, существует предельная толщина получаемого порошкового слоя, зависящая от величины заряда частиц в слое. Чем больше заряд, тем меньше предельная толщина слоя порошка.
При нанесении порошкового слоя на изделия сложной формы есть ряд особенностей в выборе режимов работы распылительного оборудования.
Процесс нанесения порошкового слоя на изделия осуществляется в установках нанесения покрытий, состоящих из окрасочных камер и систем рекуперации порошка.
Процесс формирования покрытия.
В процессе формирования покрытия из нанесенного порошкового слоя создается монолитное качественное покрытие на поверхности изделия.Чаще всего процесс формирования покрытия осуществляется путем нагрева порошкового слоя до состояния его оплавления с образованием монолитного слоя. Нагрев изделия в печи оплавления и полимеризации осуществляется до температуры 140-220 °С в зависимости от вида краски. При последующей обработке в результате отверждения (для термореактивных материалов) или охлаждения (для термопластичных материалов) слоя образуется твердая пленка.
Процесс оплавления проходит в несколько стадий:
? сначала порошок проходит вязко-текучее состояние;
? затем проходит сплавление частиц порошка с образованием монолитного слоя;
? одновременно со сплавлением происходит смачивание покрываемой поверхности и растекание расплава полимера;
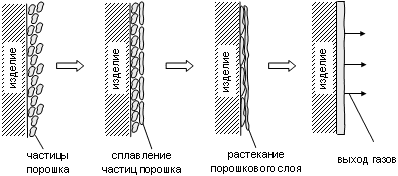
Отверждение покрытий на основе термореактивных материалов происходит в процессе теплового воздействия и длится вполне определенное время. Каждому покрываемому изделию соответствует оптимальный режим отверждения. Охлаждение покрытий на основе термореактивных материалов не влияет на свойства покрытия.
Для термопластов режим и среда охлаждения во многом определяют качество покрытия. В качестве охлаждающего агента используют воду, минеральные масла, применяют охлаждение на воздухе.
Для формирования покрытия используют:
? конвективную теплопередачу тепла от нагретого воздуха к изделию с порошковым слоем (конвективные печи). Оплавление порошкового слоя происходит с внешней стороны, что затрудняет выход газов из слоя. Данный способ обладает большой универсальностью и не зависит от формы изделия, но имеет повышенные энергетические затраты;
? инфракрасный нагрев изделия с порошковым слоем. Оплавление порошкового слоя происходит с внутренней стороны, что облегчает выход газов из слоя. Способ обладает низкими энергетическими затратами, но пригоден для изделий простой конфигурации.
- За более подробной информацией обращайтесь: